Screen printing is a technique for transferring designs onto a variety of materials, ranging from textiles to paper and plastic. One of the most important factors in getting an excellent and durable print, despite the relative ease of processing, is the type of ink to be utilized. The right ink not only makes the print look that much better but also influences its durability, texture, and tactility. Thus, if you’re just starting with screen printing or if you want to improve your skills, knowing about the different kinds of inks available will help you make the best decision for your project.
In this article, we will describe different types of inks commonly used for screen printing, their advantages, disadvantages, and recommendations for use. With this guide, you can confidently make informed decisions about inks whether you are printing your latest designs on t-shirts, posters, or advertising materials!
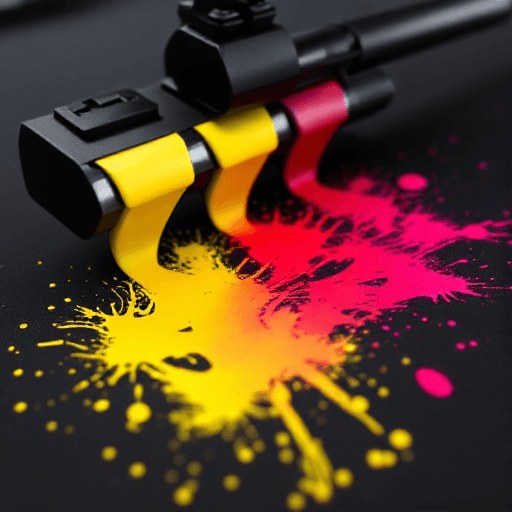
Table of Contents
Introduction to Screen Printing Inks
Screen printing is a process in which ink is pushed through a screen onto a substrate, normally fabric, paper, or the like. Ink plays a serious role in quality, feel, and durability of the print. There are various types of inks available for different applications, each formulated to accommodate specific materials, design intricacies, and production environments.
This guide will take you through an in-depth study of the most common types of inks used in screen printing, their characteristics, advantages and disadvantages, and specified applications. Whether you are a competent screen printer, a hobbyist, or a business owner wanting custom designs, hopefully, this article will guide you to make the right choice for your project regarding inks.
Types of Screen Printing Inks
Various types of inks are used in screen printing, all of them having properties that make them more or less suitable for certain applications. Let us take a look at the most popular options:
Plastisol Ink
Plastisol ink is the most popular type of ink for screen printing. It is almost exclusively used for t-shirt printing. It is an oil-based ink that stays wet until heat is applied. Hence, it can be called a very versatile and durable ink. Plastisol inks come in brilliant colors with great opacity; they can be used to print on both light and dark fabrics.
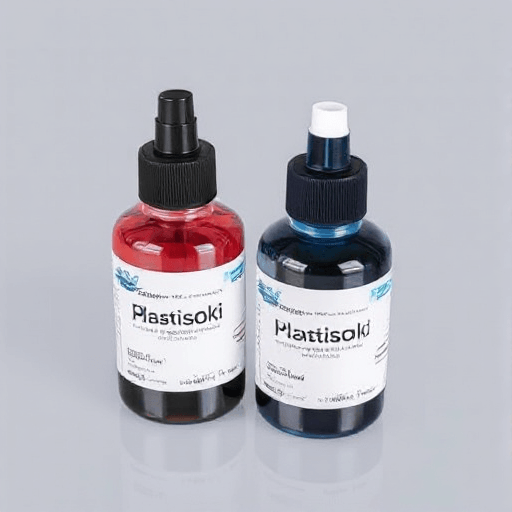
Advantages of Plastisol Ink:
- Durability: Plastisol prints are highly resistant to fading, cracking, or peeling, especially when cured properly.
- Versatility: Works on a variety of materials, including cotton, polyester, and blends.
- Vibrancy: Offers rich, bold, and opaque colors that stand out, even on dark fabrics.
- Easy to Handle: Plastisol ink remains workable for long periods before being cured, making it easier to work with.
Disadvantages of Plastisol Ink:
- Environmental Impact: Plastisol ink contains PVC (polyvinyl chloride) and phthalates, which have raised environmental concerns due to their non-biodegradable nature.
- Stiffness: Some users find that prints made with plastisol ink can feel thick or rigid, particularly when layered or used on heavy fabrics.
Water-Based Ink
Water-based inks remain an environmentally friendly alternative to plastisol. Unlike plastisol, which is cured by heat, a major solvent of the water-based ink is water. This ink, too, may be employed for printing on lighter fabrics, such as cotton, with a soft, breathable print result.
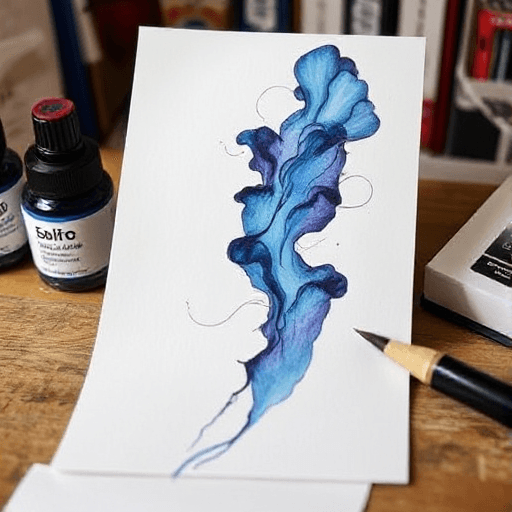
Advantages of Water-Based Ink:
- Soft Feel: Water-based ink produces prints with a soft, smooth texture that feels more like part of the fabric itself.
- Breathability: The ink allows fabrics to breathe, which is particularly beneficial for clothing worn in warmer climates.
- Eco-Friendly: Water-based inks are less harmful to the environment because they don’t contain PVC or other harmful chemicals.
- Excellent for Fine Detail: Water-based inks are ideal for detailed prints and smaller designs.
Disadvantages of Water-Based Ink:
- Limited Opacity: Water-based inks may not be as opaque as plastisol inks, especially on dark-colored fabrics, requiring the use of underbase layers.
- Fast Drying Time: Water-based inks can dry too quickly on the screen, leading to clogs or print defects if not carefully managed.
- Not Ideal for Synthetics: It can be difficult to achieve good results on synthetic fabrics like polyester, as water-based inks may not bond well.
Solvent-Based Ink
Solvent-based ink is basically used for printing on non-porous substrates like plastic, metal, or glass. It works by dissolving pigments in organic solvents, ensuring fast drying. These inks are excellent for hard surfaces, where prints are expected to be durable while having good adhesion and opacity.
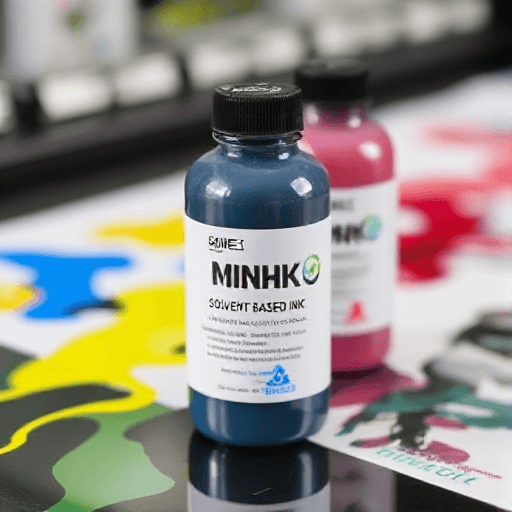
Advantages of Solvent-Based Ink:
- Adhesion to Non-Porous Surfaces: Solvent-based inks adhere well to materials that water-based inks cannot, such as plastics, glass, and metal.
- Durability: The prints are highly durable and resistant to fading, wear, and weathering.
- Fast Drying: Solvent-based inks dry quickly, speeding up the overall production process.
Disadvantages of Solvent-Based Ink:
- Environmental Concerns: Solvent-based inks emit volatile organic compounds (VOCs), which can be harmful to both the user and the environment if proper ventilation isn’t provided.
- Odor: The strong odor from solvent-based inks can be unpleasant and may require specialized equipment for ventilation.
- Limited Fabric Use: Solvent-based inks are not ideal for fabric printing and are better suited for hard surfaces.
Discharge Ink
Discharge ink is special; it removes the dye of the fabric and replaces it with the colour of the ink. It is particularly useful for printing on dark fabric, preferably cotton. Discharge inks usually provide soft prints that feel right on the fabric.
Advantages of Discharge Ink:
- Soft Prints: Discharge ink creates extremely soft prints, ideal for designs that require a natural, fabric-like feel.
- No White Underbase: Unlike traditional inks, discharge inks do not require a white underbase for dark fabrics, making the prints look more integrated into the fabric.
- Eco-Friendly: Discharge ink is considered more environmentally friendly because it does not contain harmful chemicals like PVC.
Disadvantages of Discharge Ink:
- Limited to Cotton: Discharge ink works best on natural fibers like cotton and is not recommended for synthetic fabrics like polyester.
- Difficult to Control: The discharge process requires careful monitoring, as inconsistent results can occur, especially with darker fabrics.
- Specialized Process: Requires specific chemicals and curing equipment, which can make the process more complicated than other types of screen printing.
UV Ink
UV ink gets cured under ultraviolet (UV) light. The ink is commonly used on rigid substrates such as plastic, glass, and metal. UV inks tend to dry quickly and allow vibrant prints.
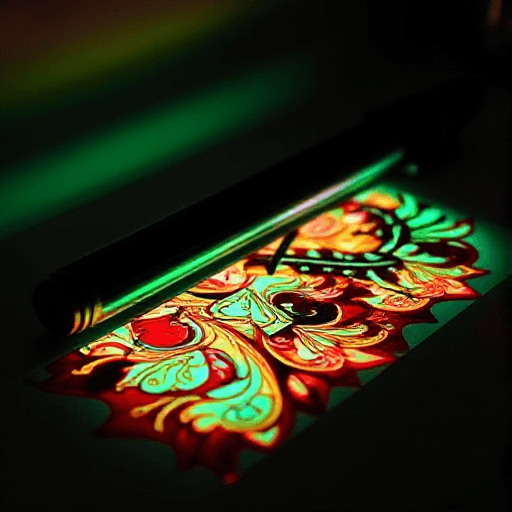
Advantages of UV Ink:
- Fast Curing: UV ink dries almost instantly when exposed to UV light, which accelerates the production process.
- Durability: UV prints are highly resistant to fading, scratching, and environmental wear.
- Vibrant Colors: UV inks produce sharp, crisp colors that look vibrant and glossy.
Disadvantages of UV Ink:
- Expensive Equipment: UV printing requires specialized curing equipment, which can be costly.
- Limited Fabric Use: While excellent for rigid materials, UV ink is not suitable for printing on fabrics or soft goods.
- Health Risks: UV ink contains photoinitiators, which can be harmful to health if proper handling procedures are not followed.
High-Density Ink
High-density ink is used to create textures or raised prints, which is mostly for logos, designs, or prints requiring a 3D effect. They work especially well for specialty printing.
Advantages of High-Density Ink:
- Raised Texture: High-density inks are ideal for creating prints with texture or a 3D effect, adding dimension to the design.
- Unique Effects: Perfect for designs that need to stand out, such as logos or other visual elements.
- Durability: These prints are often more durable and resistant to wear.
Disadvantages of High-Density Ink:
- Requires Special Equipment: High-density printing requires specialized screens and equipment, which can add complexity and cost to the process.
- Limited Design Flexibility: High-density inks may not be ideal for intricate or fine-detail designs, as they are better suited for bold, solid shapes.
Factors to Consider When Choosing Screen Printing Inks
Several factors need to be put into consideration when choosing the best ink for your project:
Material Type
Different inks work better on different materials. Here are some examples:
- Cotton: Soft and breathable prints on cotton fabric would work good with water-based or discharge inks.
- Polyester: Plastisol inks are mostly preferred for polyester and other synthetic substrates due to their durability and opacity.
- Hard Surfaces: Good inks for printing on hard materials would be anything UV or solvent-based.
Design Complexity
Your design complexity will have an influence on the type of inks to choose. For intricate detailing or gradients, water-based inks may be a nice pick. However, for some other straightforward bolder prints, plastisol inks are bound to deliver any opacity and brightness required.
Opacity
If you are printing on dark fabrics, you’ll need an ink that offers high opacity. Plastisol ink excels in this regard while water-based ink may require an underbase layer to achieve similar opacity.
Durability
Think about the lifespan required of this print. Because of superior wearability attributes, plastisol ink becomes an acceptable choice for items subjected to relatively heavy washing like T-shirts. Water-based may not trump plastisol in the long run, especially on synthetic fabrics.
Environmental Impact
If your project is eco-friendly, water-based and discharge inks are the best options. They are more environmentally friendly compared to plastisol and solvent-based inks.
Advantages and Disadvantages of Each Ink Type
Ink Type | Advantages | Disadvantages |
---|---|---|
Plastisol Ink | Durable, versatile, vibrant colors | Environmental concerns, stiff feel |
Water-Based Ink | Soft feel, eco-friendly, breathable | Limited opacity, fast drying time | | Solvent-Based Ink| Adheres to non-porous surfaces, durable | Strong fumes, environmental concerns | | Discharge Ink | Soft prints, great for dark fabrics | Limited to cotton, requires special process | | UV Ink | Fast curing, vibrant colors, durable | Expensive equipment, not for fabrics | | High-Density Ink | Raised texture, unique effects | Requires special equipment, limited design flexibility |
Best Inks for Different Materials
Choosing the right ink depends heavily on the material you are dealing with, for the following are some recommendations:
- Cotton: Water-based and discharge inks work well, offering a soft, breathable print.
- Polyester: Plastisol ink is the best choice, offering opacity and durability.
- Blends: For blended fabrics, a combination of plastisol and water-based inks can deliver excellent results.
- Rigid Surfaces (Plastic, Glass, Metal): UV and solvent-based inks are the ideal choice for these materials.
How to Maintain Screen Printing Inks
Good maintenance of inks and equipment forms part of high quality-high longevity print jobs. Here are some points:
- Storage: Store the inks in a cool and dry place so that they don’t dry out or separate before time.
- Mixing: Keep stirring the ink at intervals to maintain a uniform texture.
- Cleaning: Clean screens and equipment immediately after use to prevent ink blockage.
How to Choose the Right Ink for Your Screen Printing Project
Select an ink for screen printing according to your durability requirements, desired feeling, green considerations, and compatibility with the materials. Other considerations include opacity and dry-times and if your designs require any special effects like textured prints or raised prints.
Conclusion
The type of ink you select for your screen printing project can significantly influence the end result. Plastisol, water-based, solvent-based, discharge, UV or high-density ink – each has its own benefits and limitations. An understanding of these ink types, material compatibility, complexity of design, and environmental concerns will enable ensuring that the prints will live up to expectations for many years to come.
FAQ: Common Questions About Screen Printing Inks
What is the best ink for t-shirt printing?
Plastisol ink is usually the best choice for t-shirt printing because of its durability, vibrant colors, and versatility.
Can I use water-based ink on polyester?
Water-based ink is not ideal for polyester, as it typically lacks the opacity or durability required. Plastisol ink is best suited for synthetic fabrics.
How long do prints made with plastisol ink last
Prints made with plastisol ink may last many washes without fading or cracking, especially if properly cured.
Is discharge ink safe to use?
Discharge ink is generally safe with good handling practices, but it does require specific chemicals and curing equipment to ensure consistent results.
What is the environmental impact of solvent-based ink?
Solvent-based inks emit volatile organic compounds (VOCs) that are harmful to both the user and the environment. Proper ventilation and protective equipment are thus required.